The Future of Supply Chain: How to automate purchase orders and optimize your supply chain

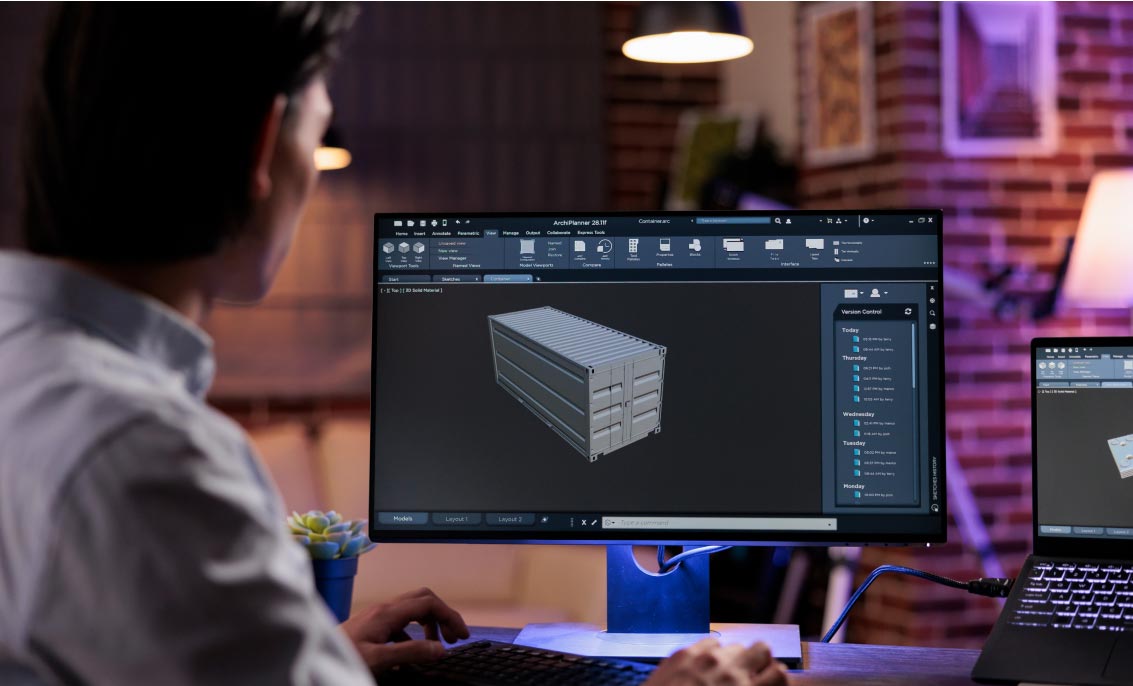
“This article will not age well!”
That is what executive leaders and supply chain practitioners should take away after reading this article. In 5 years, this article will be old news because either you or your competitors will be using Artificial Intelligence (AI) and Machine Learning (ML) to automate and optimize your purchase orders. The future tools to automate your supply chain are already available – those who wait to adopt modern AI and ML tools will quickly fall behind their competition.
Whether we call our present situation more uncertain, or simply faster-moving than ever before, every organization is required to act more dynamically. Gone are the days when you could calculate safety stocks with a simple Excel spreadsheet once a year, or rely on static, non-intelligent ERP systems for setting reorder quantities and manually place purchase orders.
Humans are not capable of processing large and complex data inputs to make timely decisions. Our role as humans is shifting from clicking buttons and expediting orders to creating a digital strategy and overseeing algorithms. The faster your organization makes the transition, the faster it will reduce stock-outs and optimize inventory, and in turn, increase margins.
Throughout this article, I will describe practical steps to develop a supply chain digital strategy and implement automated purchase order solutions.
Above all else, adhere to these best practices for a strategic approach to transforming your supply chain:
- Agree on your strategy and leadership commitment.
- Know that there is required cultural change for supply chain teams and leadership.
- Emphasize communication, clarity, and transparency.
- Simplify your first steps with concrete milestones.
- Train and support your supply chain team during this process.
- Make your algorithms into a white box solution, as opposed to a black box where calculation processes and results are not understood by the supply chain team.
- If you are working with consultants, make sure to identify the core knowledge that needs to remain in-house.
- Establish KPIs and measure improvements.
There are two key areas where organizations are more prone to making mistakes when transforming their supply chain.
The first is a poor transition from consultants to employees. Recently, I was working on a supply chain automation project for a midsize Industrial company. The company never transitioned a deep understanding of the algorithm from the consultants to the employees, resulting in supply chain disruptions for 3 months.
The second common mistake is measuring the wrong KPIs, which can result in optimizing incorrect algorithms. For example, minimizing stock-out for unimportant products will add unnecessary inventory and will not improve overall profitability. As a general rule, financial metrics are the best indicators of your improvements.
Now, are you ready for action? Here are project steps that will help you get started automating your supply chain. Some steps will need to be custom-tailored for your organization, but most of them will follow this logic:
- Create a buying category segmentation. Pick one small buying category to start the process. I recommend a simple category to get started. This will ensure a more efficient learning process and reduce risk.
- Establish clear service levels for this category or individual parts. This is important because the AI tool can be trained to monitor, predict, and enhance performance against these predefined service levels.
- Identify sources and historical data. Part POs, minimum order quantity, orders, production schedule, cost, item master info, vendors, lead time variations, forecast if available, margins, and so on.
- Clean the source data. It’s important to understand outliers, warranty/quality returns, scrap, and other data integrity issues.
- Feed data sets to the AI tool.
- Develop guardrail limits and alert methodologies.
- Develop dashboards for monitoring.
- Train, validate, and optimize AI models. This task is the essence of the entire project which will require supply chain and AI expertise.
- Create output connections to the ERP system.
- Establish an initial approval process. This will be removed once the model is properly optimized, and the process is running smoothly.
- Repeat with other product segments.
Following these strategies and the operational checklist will derisk the transition to automation. If an organization adopts the above strategies and approach it will experience the following benefits:
- Ability to process large amounts of data, enabling better decision making – in this case, placing purchase orders at the right time and in the right quantity.
- Improvements to calculating stock-out risks
- Increased customer satisfaction and reduction of production disruptions, resulting in improved margins, better cash flow and optimized inventory.
- Reduced stress on buying teams, eliminating the non-value-added transaction burden. Your supply chain experts will be able to focus on strategic sourcing, negotiation, and strategy rather than non-engaging transactional tasks.
The methodology may vary based on the company’s profile, but the overall process will remain the same. For example, a distribution company with a multi-echelon supply chain will have a more complex solution compared to a single-facility manufacturing company, but every company can get started by testing and iterating with the standardized methodology shared in this article.
The time to start your digital transformation is now, and all of the tools are already available.
Find supply chain Experts now.
Let’s TalkMeet the Author
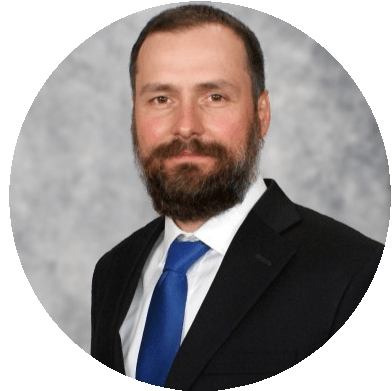
Borko is a Chicago-based independent consultant offering his services on the Catalant platform. Borko focuses on supply chain/logistics and operations improvements. He supports executive leadership that needs clear solutions in a complex environment where data is not always 100% clear. His skills are focused mostly on projects that include supply chain/logistics optimization, forecasting/demand planning, S&OP, change management, aftermarket, and using analytics/data as decision making tools to improve profitability. Prior to starting his consulting practice, Borko spent 13 years at Caterpillar improving supply chain and operations processes. He worked with various companies in the US, Europe, India, Mexico, Brazil, China, and Australia.
Want to work directly with Borko? Contact us to learn how.
W