Expert Perspectives: How to Optimize Inventory Management

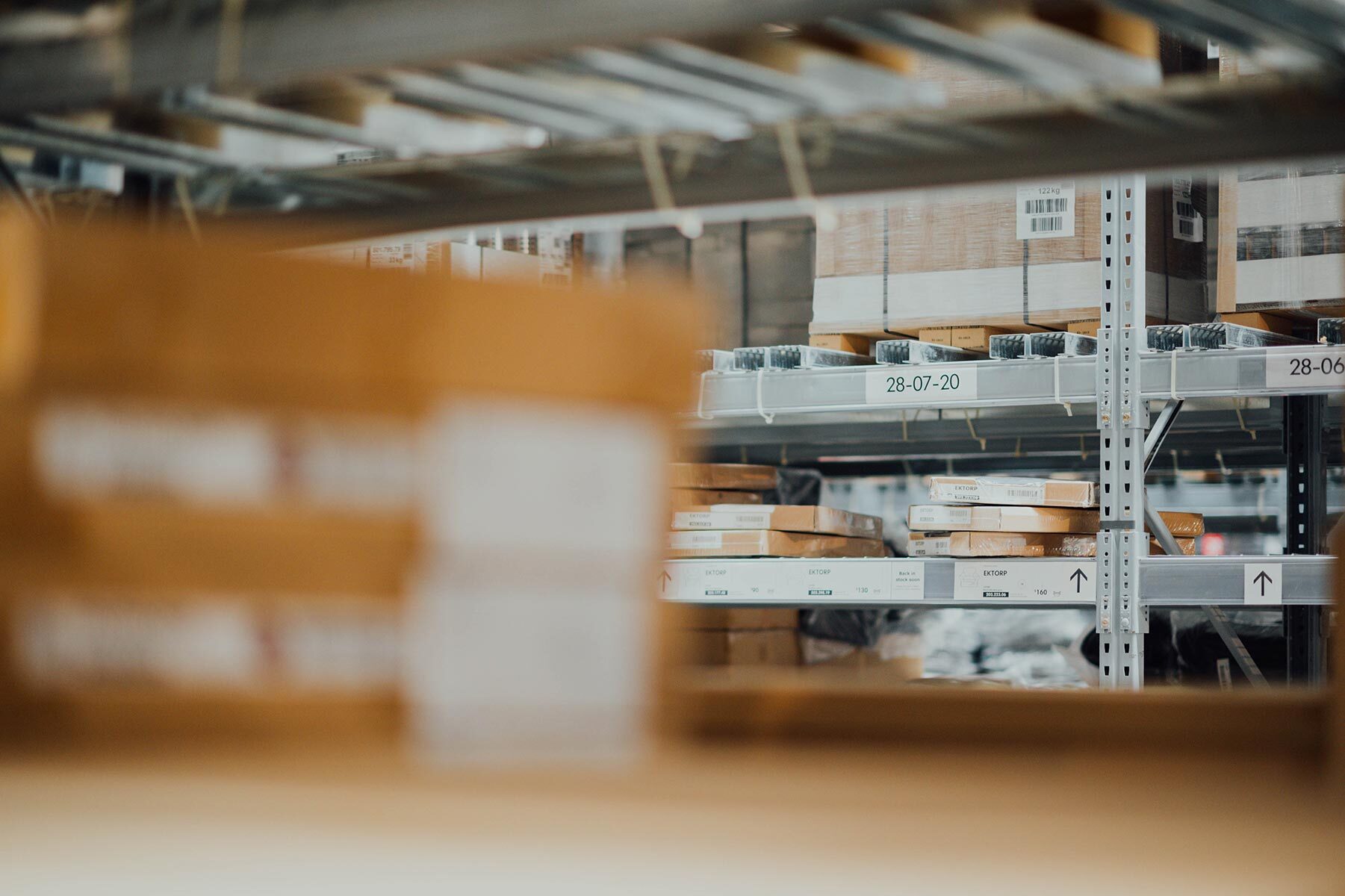
There are substantial implications and challenges for companies that don’t prioritize inventory optimization. Excessive inventory occupies valuable warehouse space, incurs high costs, and diverts capital from other essential investments. Conversely, insufficient inventory leads to stockouts, backorders, and lost sales.
The good news is that the process of how to optimize inventory management becomes seamless with the right technology, measurements, and a properly trained team.
Continue reading to learn about a few of the ways your organization can optimize inventory and achieve better operational efficiency.
What is inventory management optimization?
Inventory management optimization is the process of maintaining optimal inventory levels to meet customer demand, balance service levels and working capital, and minimize costs.
Optimizing Inventory Management
Inventory is oftentimes the biggest expense a company has, making optimization crucial for maintaining a healthy bottom line. It allows you to reduce your working capital and improve your service levels — as a result, you can utilize that money to invest in other key areas.
Inventory management:
- Frees up warehouse space and reduces operational costs.
- Reduces or mitigates slow-moving and obsolete inventory and write-offs.
- Enhances efficiency by reducing production disruptions and the need to expedite product.
Challenges Related to Inventory Management
Many companies struggle with inventory management due to inadequate technology or improper use of existing systems. Effective inventory management requires a system that updates inventory in real-time and dynamically updates parameters, such as safety stock and reorder points.
Another common problem is a lack of appropriate classification methods for inventory items. Classification is the backbone of setting up and implementing effective inventory management systems and processes. Companies without an effective classification system in place struggle to create highly efficient systems and processes that allow them to make appropriate changes in response to different stimuli, making it much more difficult to accurately forecast demand or plan for inventory fluctuations.
Lastly, your team must be trained appropriately to understand inventory management and how it affects your organization. Teams that are well-trained, and outside experts who are well-versed in inventory management, appreciate the significance of inventory optimization and may have experienced firsthand the direct impact of their actions on the bottom line.
Well-trained and experienced team members will spot potential inventory-related issues like stock discrepancies, obsolete stock, or slow-moving products, and take proactive measures before the problems escalate. Without well-trained people, your company may struggle to maintain optimal inventory levels.
Not optimizing your inventory can have major implications for your organization. You can have too much inventory — which takes up warehouse space, is expensive, and takes away capital from other needed investments — or you can have too little inventory — which causes stockouts, backorders, and lost sales.
How to Optimize Inventory Management
Here are some strategies for optimizing inventory management at your organization.
Safety Stock Level
Safety stock refers to the additional quantity of an item held in inventory as a buffer against variability in demand and lead time, ensuring there is sufficient stock on hand to meet customer needs, even in the case of an unexpected surge in demand or delay in supply chain. Here, we’re trying to minimize the risk of stockouts.
Calculating this requires an understanding of historical demand, lead time data, and Z-Score. The formula I like to use is King’s, which aims to balance the trade-off between stockout costs and carrying costs by accounting for lead time variability, demand variability, and the desired service level:
Safety Stock = Z × √[(σD^2 × LT) + (DLT^2 × σLT^2)]
- Z: Z-score, which corresponds to the desired service level (can be obtained from a standard normal distribution table or by using the NORMSINV function in Excel)
- σLT: The standard deviation of lead time
- DLT: The average demand during lead time
- σD: The standard deviation of demand
- LT: The average lead time
Lead times and demand can be volatile, so account for those swings, otherwise, you’ll have too much or too little inventory. This may require calculating safety stock at different times, under different conditions.
ABC XYZ Classification
Another important exercise is ABC XYZ classification. ABC analysis allows you to focus on products that represent your largest sales. While ABC analysis is helpful, you need to add XYZ to better estimate service rates and safety stock targets. XYZ takes into account demand uncertainty.
For example, if your highest-selling item is a seasonal item, like Valentine’s Day decor, it might be an “A” item for your company. But if it’s summer, you shouldn’t expect to have high demand for these items. An XYZ analysis would classify the Valentine’s Day decor products as a “Z” item in terms of demand variability. The combined AZ classification would prompt a savvy supply chain analyst to adopt a more dynamic inventory management strategy for Valentine’s Day decor, holding more inventory to maximize service levels in high-demand times, and adjusting stock levels and replenishment policies according to seasonality and resulting fluctuations in demand.
For ABC:
- Calculate the annual consumption value for each item by multiplying the annual number of units sold by the cost per unit.
- List the products in descending order based on their annual consumption value.
- Total your total number of units sold and the annual consumption value.
- Calculate the cumulative percentages of both.
- Determine your thresholds for splitting the data into ABC categories (typically, it will be 80% / 15% / 5%.)
For XYZ:
- Calculate the coefficient of variation for each item — standard deviation/mean x 100.
- Sort the items by increasing the coefficient of variation and accumulate the figures — items with the lowest coefficient of variation will be X, and those with the highest will be Z.
Combining the two classifications:
- Create a matrix combining the ABC and XYZ classifications, resulting in nine categories (AX, AY, AZ, BX, BY, BZ, CX, CY, and CZ).
- Each item in your inventory will now have a combined classification (e.g., AX, BY, etc.) and resulting value and demand predictability.
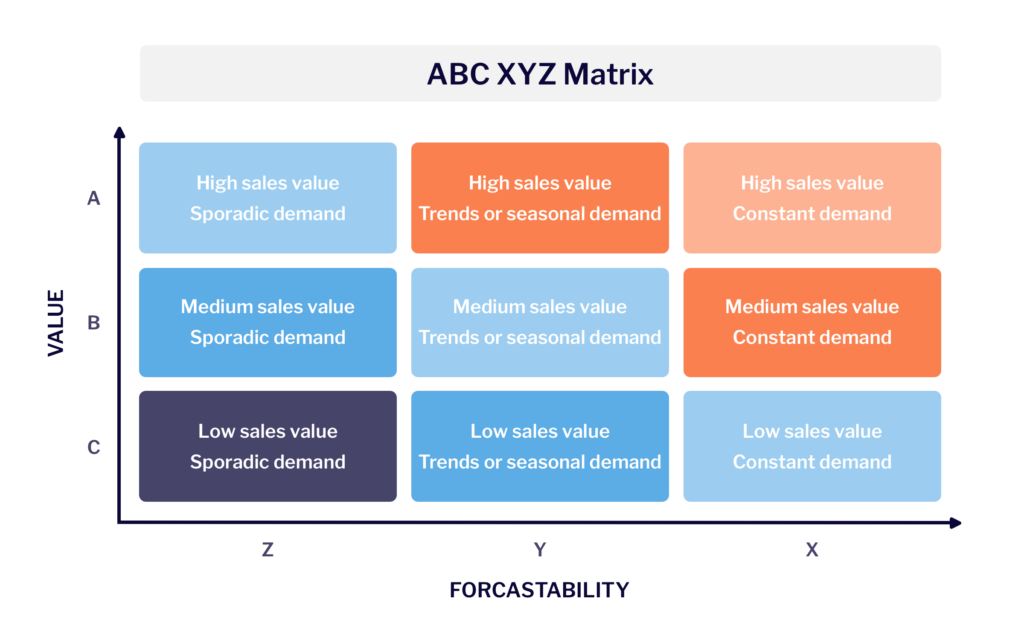
Source: https://shopup.me/model/abc-xyz-analysis/
Economic Order Quantity (EOQ)
Economic order quantity (EOQ) is a calculation designed to find the optimal order quantity for businesses to minimize logistics costs, warehousing space, stockouts, and overstock costs. EOQ is an important cash flow tool to help control the amount of cash tied up in inventory.
Remember, as demand patterns and costs change over time, it’s important to update this calculation periodically.
The EOQ formula is:
EOQ = √(2DS / H)
- Q = EOQ units
- D = Demand in units (typically on an annual basis)
- S = Order cost (per P.O.)
- H = Holding costs (per unit, per year)
The result of the EOQ formula will give you the optimal order quantity that minimizes the total inventory costs.
Minimum Order Quantity (MOQ)
Likewise, suppliers are optimizing their own inventories and costs, so you’ll want to ensure your terms are favorable. Work with your suppliers on minimum order quantity (MOQ) — the lowest quantity of product they are willing to produce or sell in a single order — and make sure that their MOQs don’t leave you with excess inventory.
Strike a balance between the supplier’s requirements and your own inventory management needs. This may involve negotiating a lower MOQ, adjusting order frequency, or finding alternative suppliers with more favorable MOQ terms.
Leveraging External Expertise for Inventory Optimization
While the strategies mentioned above are effective, implementing them can be challenging for organizations without sufficient expertise. Hiring external talent with specialized knowledge in inventory optimization management can streamline the process and ensure a higher degree of success.
Several of the strategies above rely on knowing when to recalculate a formula based on internal and external factors. An experienced partner can help identify those key moments and update models accordingly.
External experts bring fresh perspectives, up-to-date technology insights, and proven strategies that can significantly enhance your inventory management system. By partnering with external specialists, you can optimize your inventory, reduce costs, improve efficiency, and ultimately, bolster your bottom line.
Meet the Author
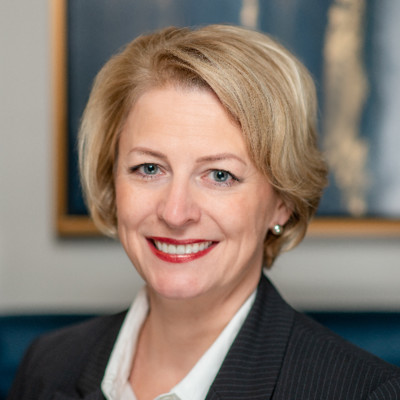
Tara is an Expert on the Catalant platform with over 20 years of experience in purchasing, sourcing, logistics, demand and supply planning, S&OP, inventory management and production. Tara is Lean Six Sigma Green Belt certified as well as AIPCS certified. She has been featured in supply chain publications like CHAIN Magazine for supply chain and sustainability contributions. Tara earned her undergraduate degree in business from Clayton State University and her MBA from Mercer University.