The Coming Revolution: How AI is Transforming Manufacturing

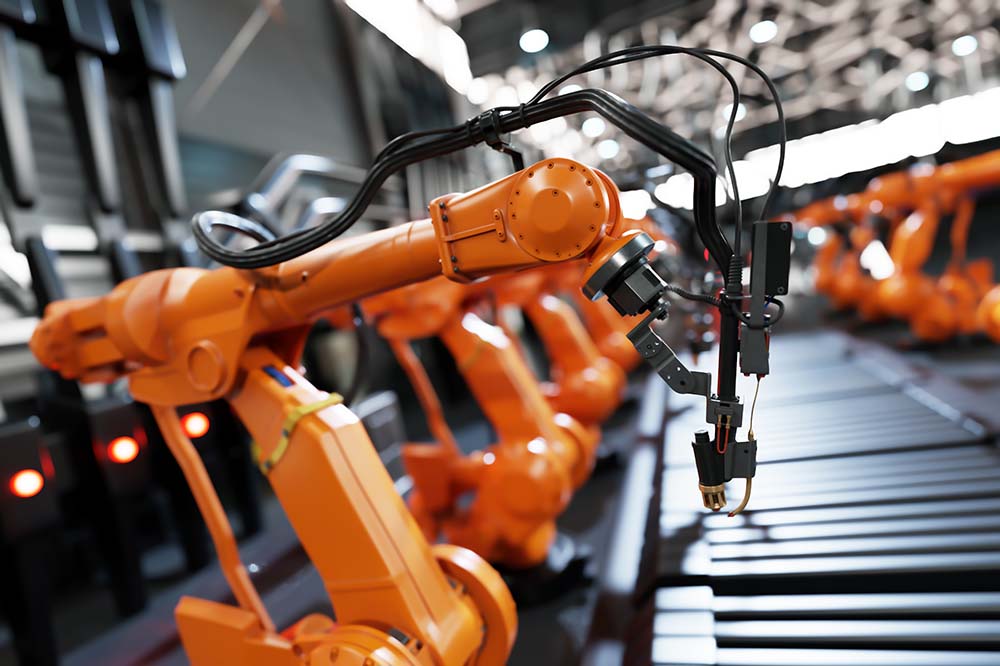
Artificial intelligence is poised to revolutionize manufacturing sooner than many industry leaders anticipate. AI isn’t coming to manufacturing. It’s already here.
While buzzwords like “generative AI” grab headlines, a more consequential force is quietly taking shape on factory floors and in planning meetings: agentic AI — systems that can reason, act autonomously, and drive outcomes based on real-time data and shifting priorities. For manufacturers, this is a once-in-a-generation opportunity to redefine how work gets done across the value chain. This will fundamentally transform how factories operate and how production is actively managed.
Two-Phase Implementation of Agentic AI
The integration of AI in manufacturing will unfold in two distinct phases, with the first already beginning to take shape.
Phase 1: Operations Planning and Scheduling
The most immediate impact of AI is being felt in planning functions — from sales and operations planning (S&OP) to production scheduling. This progression makes practical sense, as most manufacturers already have Enterprise Resource Planning (ERP) or Manufacturing Resource Planning (MRP) systems in place, with Manufacturing Execution Systems (MES) bridging to production systems. These existing platforms provide the necessary data infrastructure and real-time monitoring capabilities that agentic AI requires for optimization.
What’s changing now is the speed and autonomy with which decisions can be made. Autonomous AI agents can dynamically replan based on changes in demand, material availability, or even geopolitical events like trade tariffs or disruptions in shipping lanes. These systems don’t just optimize schedules — they learn and adapt over time, enabling continuous improvement without human intervention.
As an example, Nvidia recently announced at their Global Technical Conference (GTC) a partnership with General Motors to implement Omniverse digital twins for factory planning and, eventually, robotic operations management.
The immediate future will see AI systems updating and optimizing sales and operations plans in real time, responding overnight to changes in orders or sales activities. These systems will transmit signals from the sales end directly to operations scheduling, ensuring that costs, performance requirements, and timing are continuously optimized.
Phase 2: Factory Floor Integration
The second implementation phase—which will take longer due to infrastructure requirements—involves AI integration directly on the factory floor (not just directing operations on the floor). This goes beyond the familiar manufacturing robots in automobile plants to encompass increasingly networked machinery for metal forming, thermoforming, tube bending, and other manufacturing processes.
This machinery is being connected to MES systems that can monitor operations and issue commands based on what they observe. Beyond the attention-grabbing demonstrations of voice-commanded robots, the true value lies in the comprehensive networking of all machinery and operations throughout the factory floor.
NVIDIA’s recent moves are a sign of what’s to come: integrating digital twins, real-time data, and AI to simulate, plan, and manage factory operations. The convergence of these capabilities will unlock massive gains in productivity and agility.
The Ultimate Vision: Autonomous Manufacturing
The end goal is a manufacturing ecosystem where changes in demand or external conditions—such as new tariffs between production and selling regions, spikes in shipping costs, or disruptions to shipping lanes like recent events in the Red Sea—are automatically reflected in sales and operations plans by autonomous AI agents. These adjustments will then cascade to the factory floor operations without human intervention.
While human supervision will remain indispensable, these systems will operate autonomously and continuously, bringing about a revolution in manufacturing productivity that will transform the industry.
This isn’t science fiction. It’s a fast-emerging reality, and the organizations that move early will set the pace for the next era of industrial performance.
Catalant Can Help
The revolution is already underway. Let’s make sure you’re leading it. Catalant’s Consulting 2.0 connects forward-looking manufacturers with manufacturing experts like Byron who are enabling advanced manufacturing strategies in real-world settings — from Fortune 500 factories to high-growth supply chains. Whether you’re rethinking your planning processes, building AI use cases, or redeploying your assets to better cope with a volatile trade environment, we have the people who know the terrain.
Interested in bringing Consulting 2.0 to your firm?
Let’s TalkMeet the Author
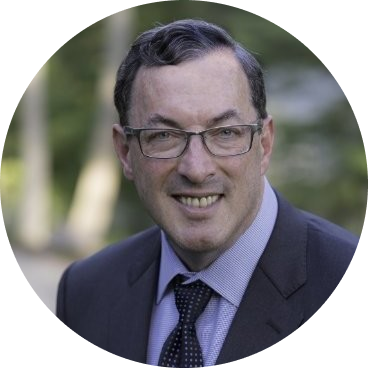
A principal at eos consulting, Byron Winn has worked with global OEMs such as John Deere and Cummins (as well as industrial suppliers deep in the value chain) to build and execute growth strategies (where to compete, how to win), manufacturing strategies (what to build where, and how), and Go To Market programs (including market mapping and segmentation; value propositions; channel and marketing strategies). He is a former fighter pilot and a Harvard Ph.D.